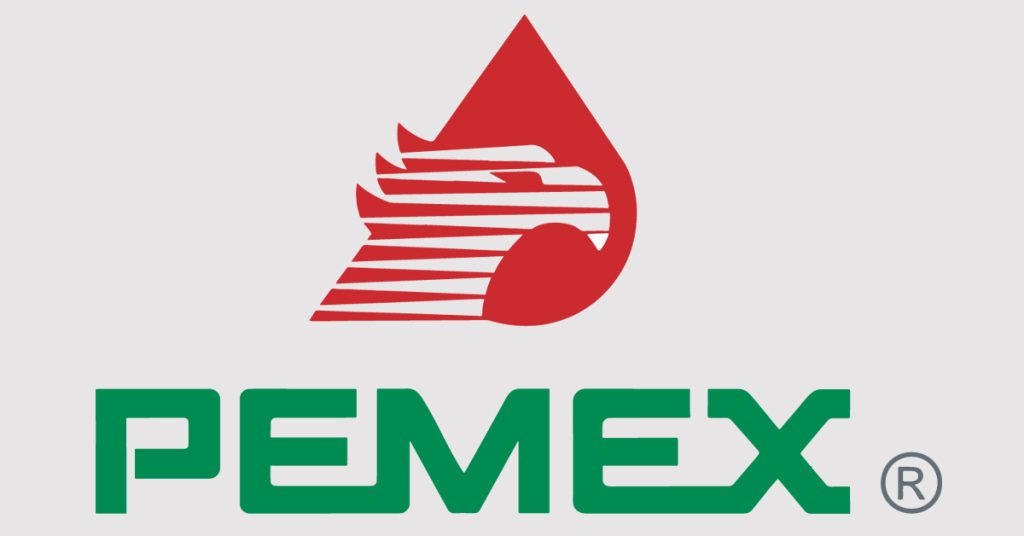
When Pemex Oil refinery located in Monterrey Mexico was experiencing problems with a 48 inch diameter process oil line they called the best in the business to handle the problem, US Pipelining.
Several sites visits to Monterrey were required by the US Pipelining team in order to establish exactly what the issues were and what exactly was causing the issues with the 8,000 foot long 48 inch diameter steel oil carrying pipe. The pipe had a low working pressure of 25psi. The pipe was able to be shut down and drained for a short period of time. This allowed US Pipelining to introduce a CCTV robotic camera system with sonar capabilities. The information that was retrieved was astounding. The data showed that the steel pipe which was installed more than 40 years ago was showing imamate signs of failure. The pipe had already been experiencing failures at certain locations.
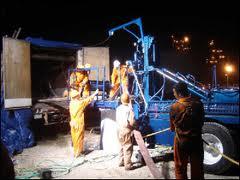
Pemex had excavated the 12ft deep pipe at these locations where they had experiencing failures and made temporary spot repairs using crude external rubber saddles wrapped around the exterior of the pipe at the problem areas. US Pipelining knew at that point that time was not on their side. This pipe was critical to the plants over all operation and could not remain off-line for more than 48 hrs. US Pipelining quickly went to work designing a plan that could be implemented right away.
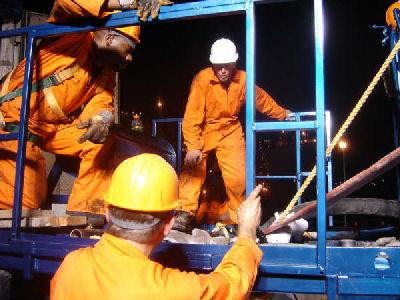
The US Pipelining crew was back on site with in 30 days to install the 8,000 feet of 48 inch diameter pressure pipe liner. Getting the materials transported from the United States in to Mexico would prove challenging. However, along with the cooperation of Pemex and the Mexican government the border crossings seemed to come together. Pemex is the only oil company in Mexico and of course government owned. The Mexican government was made aware of the urgency of this project and was more than accommodating in assisting the border crossing of the materials. Due to the critical nature of this project the Mexican government provided an escort vehicle from the border crossing in Texas to Monterrey Mexico.
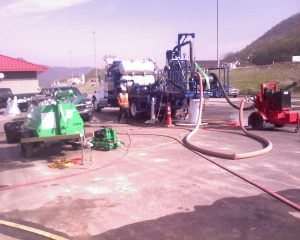
Once on site the US Pipelining team quickly went to work. A temporary bypass system was installed using welded HDPE pipe. This would allow for the plant to remain in operation through out the project. 800ft long increments of the 48inch diameter pressure liner would then be installed. Each 800ft long section would take two to three days each. As each section of liner was installed a welding crew went behind the lining crew to put the pipe back together at each section. Flanges were welded on to a 6ft long steel 48 inch diameter spool piece and set back in place at each entry location. Once the last section of liner was put in place the last spool piece was dropped in place and installed allowing the system to be put back on line immediately. All and all the installation process took 16 days .
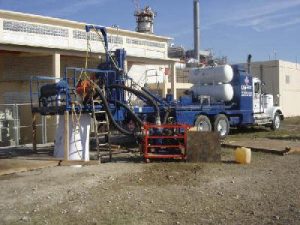